BoxMania
A robot that cuts open a box and flattens it
WHAT
-
Designed and prototyped a robot that unfolds cardboard boxes
-
Performed Failure Modes and Effects Analysis (FMEA) to refine design
-
Conducted static analysis to determine motor parameters (speed, torque)
HOW
-
Used Fusion360 to design chassis and components for robot
-
Fabricated chassis components using Laser Cutting and 3D Printing
-
Applied DFMA techniques to minimize number of 3D parts to reduce fabrication lead times
RESULTS
-
Robot successfully processed a cardboard box in 25s
-
Improved system reliability to 80% by applying FMEA techniques
SUMMARY
Cardboard packaging is essential in global commerce due to its durability, lightweight nature, and recyclability. In the U.S., about 70% of corrugated cardboard is recycled, but this rate could increase with better practices, such as properly collapsing boxes. Large heaps of un-collapsed cardboard are a common issue, especially in businesses and warehouses where workers often lack the time to break them down efficiently. Current solutions are bulky and destructive.

CURRENT BULKY SOLUTIONS - BALERS
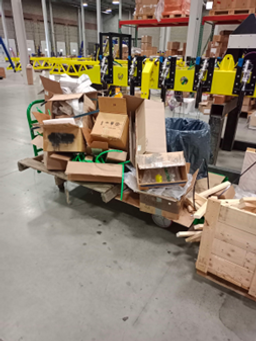
LARGE HEAPS OF CARDBOARD BOXES - FOUND DURING OUR VISITS TO NEARBY FACTORIES
We developed a box-flattening robot to automate the process of collapsing and disposing of cardboard boxes into recycling bins. Existing solutions like compactors and crushers are expensive, dangerous, and destroy boxes, making them unusable for reuse. Our goal was to fill this gap with a non-destructive, automated solution.
The BoxMania robot positions the box, cuts the tape, opens the flaps, collapses the box, and clears it from the machine. We prioritized speed, durability, user-friendliness, and non-destructive handling. Using discrete subsystems and advanced sensors, we simplified operation while reducing the risk of damage or injury.
This solution addresses the environmental challenge of cardboard waste by offering a cost-effective, automated alternative that promotes recycling and reduces the burden on businesses and waste management systems.

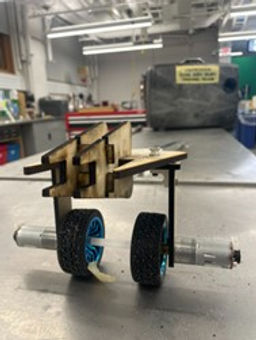
INITIAL PROTOTYPE OF FLAP OPENER
The process has three major steps:
-
Tape Cutting: A sharpened sheet metal blade is mounted on a 3D-printed adjustable slotted holder for fine height control. It is driven by a timing belt and stepper motor along a linear rail, ensuring smooth motion and precise cutting of the tape.
-
Flap Opening: Two rubber wheels, powered by DC motors, move forward into the box for 5 seconds, with a stopper limiting penetration, then rotate for 1 second to pull the box towards a flap-opening interface. Flaps are opened to at least 50°, and the wheels then reverse for 800ms, pushing the box back and resetting the opener. A weight ensures contact between the wheels and cardboard, and the rod moves smoothly on bearings to account for small height changes.
-
Flattening: A 3D-printed extruded trapezoid, driven by a timing belt and stepper motor, pushes the box into an angled board. This collapses the box, which is then fully expelled from the enclosure into a recycling bin.
